Что такое фибергласс | Блог Uzumeti
Спортивное оборудование, а в частности — и каркас палатки часто изготавливается из так называемого фибергласса. Из него изготавливают в т.ч. и дуги для палатки. Что же такое фибергласс и какие он имеет преимущества перед другими материалами в обозначенной области применения?
Сам по себе фибергласс – это композитный полимерный материал. Часто можно встретить такое его название, как стеклопластик.
Что такое композитный материал? Про это мы рассказывали в этом видео:
В качестве струкутрообразующей сетки используются стекловолокна, составляющие 70% от основного объема материала, а наполняющим веществом является эпоксидная смола. Получил широкое распространение во всех отраслях промышленности. Часто используется при изготовлении пластиковых окон. До этого долгое время использовался в оборонке и самолетостроении.
Очень полезно посмотреть вот это наше видео:
Это один из немногих материалов, который сочетает высокую прочность, хорошие диэлектрические свойства, диэлектрические свойства и химическую стойкость. При этом цена пластика остаётся невысокой. Этот полимер не гниет, не меняет цвет, не охрупчивается с течением времени и практически не подвержен старению.
Прочность этого материала в несколько раз выше прочности алюминия и в девять раз выше прочности ПВХ.
Если коротко перечислить достоинства данного материала, то сюда войдут низкий удельный вес, высокая прочность, широкий диапазон рабочих температур от -60 градусов Цельсия до + 80 градусов по шкале Цельсия, стойкость к агрессивным средам, плохую теплопроводность и отсутствие электрической проницаемости.
К недостаткам можно отнести пожалуй только низкие показатели модуля упругости.
Правда говорить о достоинствах и недостатках материала с точки зрения материаловедения не совсем корректно. Ведь недостаток в одном случае становится преимуществом в другом. Возьмем ту же диэлектрическую проницаемость. Было бы весело делать провода из диэлектрика, но ведь мы этого не делаем. Правильнее будет сказать, что материал не применим для изготовления проводки в доме. Такая же ситуация и с остальными свойствами.
Сравнение механических свойств алюминия и фибергласса
Теперь подойдем непосредственно к численным значениям и показателям табличных значений механических свойств. Поскольку вторым типичным материалом для изготовления каркасов палаток является алюминий, бегло сравним композитный полимер именно с ним.
Например, если сравнивать алюминиевый сплав (на данный момент не столь важно какой именно, все показатели будут в указанных порядках) и фибергласс (опять же, возьмем общего представителя вида), то мы имеем следующие показатели:
Разрушающее напряжение МН/м2: 410 — 1180 у стеклопластика против 80 – 430 у алюминия
Модуль упругости при растяжении, ГПа: 21-41 у фибергласса, против 70 у алюминиевого сплава.
Что означает этот набор значений для обычного пользователя?
Удельная прочность стеклопластика выше прочности алюминиевых сплавов почти в два раза, из чего следует, что при изделии с одинаковой прочностью в случае использования стеклопластика будет весить в два раза меньше, чем изделие с такими же свойствами из алюминия. Т.е. при прочих равных, каркас палатки из фибергласса будет в два раза легче алюминиевого, а прочность будет одинаковая.
Далее, рассмотрим показатели разрушающего напряжения. Или предела прочности. В таблице приведены диапазоны значений. При их анализа получается, что неправильно подобранная марка стеклопластика окажется аналогична хорошему алюминиевому сплаву. Здесь также фиберглассовый каркас для палатки вырывается вперед по значениям свойств если брать средние показатели.
Остаётся модуль упругости. Если упростить формулировку – это то значение нагрузки, которое может выдержать материал без разрушения или насколько хорошо материал гнётся. Здесь стеклопластик проигрывает алюминию. Т.е. каркас из алюминиевого сплава будет лучше воспринимать деформации.
Какими свойствами обладает каркас палатки из фибергласса?
Каркас палатки из стеклопластика имеет большую прочность, меньший вес, но при этом способен деформироваться в меньших пределах. При этом остаточная деформация будет минимальной, так как материал не склонен к пластической деформации из-за его высокой прочности. Соответственно – это более хрупкий материал и не любит изгибы. Вопреки распространенному мнению, холод никак не сказывается на свойствах этого материала, т.к. палатки используются заведомо в меньшем интервале температур. Почему же ломается каркас из фибергласса на морозе у зимних палаток? Происходит это по той причине, что сам по себе стеклопластик не любит деформации и если они достигают придельных показателей (которые в разы меньше, чем для алюминия, способного к пластической деформации) просто ломается. Летом такой каркас сломался бы также.
Что в итоге лучше, фибергласс или алюминий?
Конечно же, фибергласс – материал инновационный и перспективный. Но неправильная работа с этим материалом делает его менее привлекательным для покупателя. Производители часто выбирают самые дешевые сорта пластика, которые обладают худшими свойствами и при этом сохраняет высокую хрупкость. Также нужно учитывать, что одинаковое построение каркаса из алюминия и фибергласса не возможно. На данный момент для рядового пользователя, а особенно – для пользователя зимней палатки, лучше выбирать алюминиевый каркас. Он ремонтопригоден и, в любом случае, будет обладать большей пластичностью – т.е. лучше гнуться без повреждения. Но при этом алюминий будет тяжелее и дуги будут со временем «проседать» (т.е. придётся выгибать их в обратную сторону для выпрямления руками).
Заключение и выводы
Правильным подходом в выборе материала каркаса является анализ каждой конкретной конструкции у каждой модели. В нашем случае, это возможно только по отзывам пользователей и по непосредственным ощущениям. Говорить однозначно, что палатка с алюминиевым каркасом будет лучше или хуже, чем палатка с каркасом из стеклопластика, неправильно. Для каждого конкретного случая нужно иметь четкое понимание механических показателей данной марки материала и предельных деформаций в данной модели. Иными словами, мы ни в коем случае не исключаем, что среди фиберглассовых каркасов есть надежные и очень достойные модели, поскольку при правильном просчёте и подборе материала – стеклопластик лучше алюминия. Среди бюджетных палаток такие не встретишь.
Ну и для окончательного понимания актуальности использования фибергласса для каркаса палаток и его достоинств, приводим диаграмму из английского журнала, где указано распределения материалов и их типов, которые использованы для изготовления самолёта типа Боинг. Обратите внимание — наша позиция выделена зеленым. Т.е. при правильном подходе, этот материал подходит для самолетостроения.
А в этом примере, найденном на одном из форумов, производитель сделал что-то неправильно и каркас сломался. По убеждения пользователя, добавившего фотографии, сломался из-за ветра. Значит предел допустимой деформации был превышен. Вероятно, не рассчитали размер купола и дуги для палатки лопнули от изгиба.
Есть и ещё один важный момент. Часто производитель использует какой-нибудь самый дешевый пластик с низкими показателями мех.свойств и выдает его за дорогой стеклопластик. Определить на глаз это практически невозможно. Но в итоге складывается впечатление, что плохим является материал, указанный в характеристиках изделия.
Вас также может заинтересовать
Фиберглас
Фиберглас [англ. fiberglass
Фиберглас используется в производстве уже довольно давно.
Материал представляет собой композит полимера и стекловолокна, который в 3 раза прочнее алюминия и в 9 обычного ПВХ
Фибергласс — стеклонаполненный материал (70% стекловолокна) на основе полиэфирных смол, обладает прочностью и долговечностью металла,биологической стойкостью полимера (не гниёт, не меняет цвет, не становится хрупким).
- Прочность в 9 раз выше ,чем у ПВХ
и в 2-4 раза выше, чем у алюминия.
- Термическое расширение и сжатие стекла, поэтому нет деформаций.
Фибергласс многие годы широко использовался в оборонной промышленности, самолетостроении, кораблестроении и других областях, где к материалу предъявлялись повышенные требования по прочностным характеристикам, теплосбережению, устойчивости к агрессивным средам, сохранению свойств при резких колебаниях температур, долговечность, экологичность, словом, все требования, которые мы предъявляем к современным материалам.
Именно поэтому материалы на основе фибергласа активно используют, например, в автомобилестроении, при производстве любых элементов, которые должны выдерживать большие механические нагрузки.
Использование фибергласа повышает прочность изделия, что в свою очередь позволяет избежать таких проблем, как перекос и деформации в процессе эксплуатации.
Фиберглассовый каркас не требует практически никакого ухода, на них не остается царапин, сколов, следов коррозии.
Свойства фибергласса
Фибергласс обладает многими очень ценными свойствами, дающими ему право называться одним из материалов будущего. Ниже перечислены некоторые из них.
- Малый вес. Удельный вес фибергласса колеблется от 0,4 до 1,8 и в среднем составляет 1,1 г/см3. Напомним, что удельный вес металлов значительно выше, например, стали-7,8, а меди-8,9 г/см3, дюралюмина -2,8 г/см3. Таким образом, удельный вес фибергласса в среднем в пять-шесть раз меньше, чем у черных и цветных металлов, и в два раза меньше, чем у дюралюмина.
- Диэлектрические свойства. Фибергласс является прекрасным электроизоляционным материалом при использовании как переменного, так и постоянного тока.
- Высокая коррозионная стойкость. Фибергласс, как диэлектрик, совершенно не подвергаются электрохимической коррозии. Фибергласс обладает стойкостью к различным агрессивным средам, в том числе и к воздействию концентрированных кислот и щелочей. Для фибергласса характерно сочетание высоких атмосферо-, водо- и химстойкости.
Фибергласс — это… Что такое Фибергласс?
Стеклопла́стик — вид композиционных материалов — пластические материалы, состоящие из стекловолокнистого наполнителя (стеклянное волокно, волокно из кварца и др.) и связующего вещества (термореактивные и термопластичные полимеры).
Стеклопластик это очень перспективный лёгкий материал с заданными свойствами, который имеет большую область применения. Стеклопластики обладают теплопроводностью дерева, прочностью стали, биологической стойкостью, влагостойкостью и атмосферостойкостью полимеров, не имея недостатков, присущих термопластам.
Стеклопластики уступают стали по значениям предела прочности, но в 3,5 раза легче и превосходят стали по удельной прочности. Если изготовить равнопрочные конструкции из стали и из стеклопластика, то стеклопластиковая будет в несколько раз легче.
Стойкость к действию химикатов и эксплуатационные показатели стеклопластика продемонстрированы в прошедшие 60 лет с успешным использованием разнообразных изделий из композитов в сотнях различных химических средах. Практический опыт был дополнен систематической оценкой соединений, подвергнутых большому количеству химических сред в лабораторных условиях. К изделиям из химически стойкого стеклопластика относятся:
- напорные и безнапорные трубопроводы для транспортировки агрессивных жидкостей и сред,
- емкости как горизонтальные, так и вертикальные для хранения и транспортировки агрессивных жидкостей,
- желоба для подачи электролита,
- секции охлаждающих градирен, напорные коллекторы
- газоотводящие стволы дымовых труб,
- травильные и электролизные ванны.
- вентиляционные системы для удаления паров вредных веществ от технологического оборудования
Производители стеклопластика
Wikimedia Foundation. 2010.
Блог о зонтах на сайте ZontShop.ru
26.05.2016
Тематика: Познавательно
Современные зонты — это образец стиля, качества и надежности. Аксессуары сегодняшнего дня производятся при непосредственном сотрудничестве с высокими технологиями и лучшими научными разработками. Это касается не только купола, который делают из полиэстера, поливинила, сатина, эпонжа, шелка, но и каркаса с применением такого суперсовременного материала как фибергласс.
Легче стали, тверже алюминия
Много лет назад производители задумались на тему, как помочь некоторым людям полюбить зонтики. Ведь аксессуар прекрасный элемент как женского, так и мужского гардероба — не только защищает от дождя, но и многое может рассказать о своем хозяине. По зонту легко определить, к какой прослойке общества относится человек, какой образ жизни ведет, сколько зарабатывает, какой у него стиль, вкус и так далее… Не зря же, деловые люди предпочитают строгие полностью автоматические трости с деревянной ручкой J-образной формы — это дорого и солидно, а юные студентки выбирают экземпляры в 3-4 сложения, яркие, легкие, чтобы помещались в студенческом рюкзачке.
Но почему же тогда до сих пор есть те, кто носит капюшоны? Говорят, так легче и надежнее…
И тогда мировые бренды обратились к науке в поисках материала, который бы сохранил прочность корпуса на уровне стали, но при этом уменьшил вес на уровне алюминия. Таким материалом в идеальном соотношении оказался фибергласс — новейшая в 50-е годы разработка ученых оборонной промышленности.
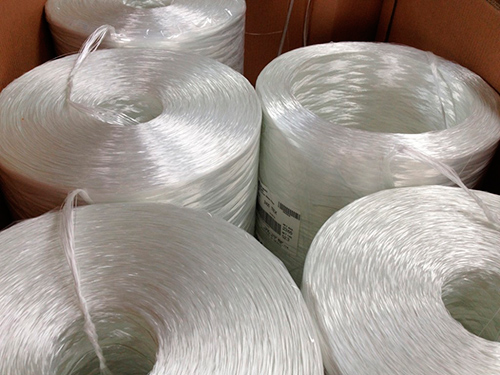
Дешево и весело
Фибергласс, или проще говоря, стеклопластик, производится, как наверное уже стало понятно, из нитей стекловолокна, пропитанных специальными смолами и переплетенных между собой разными способами, от чего зависит плотность, вес, а также износостойкость итогового результата.
В отличие от карбона, про который блог магазина ZontShop.ru уже рассказывал, фибергласс обладает качествами, особенно привлекательными для производителей — это прочный и при этом относительно недорогой композит.
Первое время массовое потребление тормозилось главным образом из-за отсутствия широкоформатных промышленных технологий, но со временем решили и это вопрос, запустив технологию пултрузия — протягивание материала через нагретую фильеру. Этот простой метод вывел фибергласс в массы и сделал одним из самых популярных композитов в области строительства, авиационной промышленности, кораблестроения, а также всевозможных бытовых нужд.
На кончике спицы
У фибергласса есть еще одно неоспоримое преимущество — он прекрасно режется на разные формы разной толщины и поддается окрашиванию во всевозможные оттенки, устойчив изменениям температуры и механическим повреждениям. Все это как нельзя лучше устраивало крупных зонтичных производителей. Doppler первая компания, которая начала применять стеклокомпозит в своем производстве, используя его в последнем звене спиц. Благодаря чему при умеренных порывах ветра крайние спицы каркаса купола не ломаются, а только гнутся.
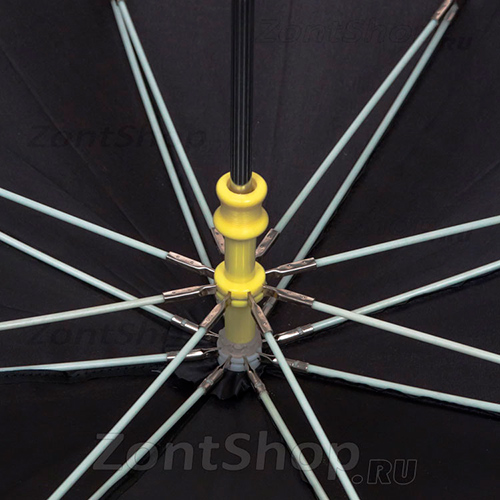
Главное, не морозиться
В природе, особенно человеческих изобретений, не бывает ничего идеального и фибергласс, безусловно, имеет свойства, которые накладывают на его использование некоторый отпечаток. В первую очередь, он плохо переносит воздействие ультрафиолета и начинает разрушаться при температуре ниже — 15 градусов Цельсия. Если с первым технологи более-менее научились справляться — покрывают композит специальной защитной обмоткой, то со вторым придется мириться, что довольно просто — помните, что зонт, со спицами из фибергласса, используют в теплое время года для защиты от солнца, дождя и мокрого снега.
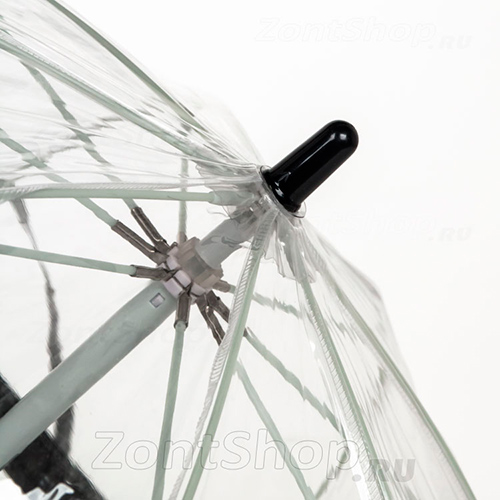
Стекловолокно или файбергласс – материал-новинка, используемый в нейл-индустрии для наращивания, укрепления и коррекции ногтей. Изготовляется из стекла с добавлением химических компонентов для придания пластичности. Материал этот очень прочный и гибкий. Он не ломается, как стекло.
Что такое файбергласс
Файбергласс — это стекловолокна, соединенные в пучок, толщиной несколько миллиметров. Отдельное волокно – прочное, гибкое и очень тонкое, как волосок, поэтому материал берут в работу именно пучками. Продается фасованным по различной длине и толщине. Чем длиннее пучок материала, тем на дольше его хватит.
Из одной упаковки файбергласса получается около 40 наращенных ногтей при пересчете на максимальную длину наращивания. Максимальная длина файбергласса для наращивания ногтей может просчитываться с помощью нижних бумажных форм для наращивания ногтей. На них есть разметка длины.
Технология новая, очень стремительно набирает популярность, и с таким же успехом на рынке появляется много подделок. Заказывай файбергласс на проверенных сайтах, с сертификатом. Лучше отказаться от китайских дешевых вариантов без отзывов, с того же AliExpress. При покупке рекомендуется обращать внимание на наличие сертификата качества. В нём должно быть указано, что данное стекловолокно изготовлено непосредственно для ногтей, имеет специальную обработку.
Популярные качественные марки с хорошими отзывами мастеров:
- O.X Nail Fiber Modelling and Extension
- Canni Fiber Glass
- GGA Professional Fiber Glass
- EzFlow Pro Fiberglass System
- Armory Nails.
Толщина
Чем толще файбергласс, тем он менее гибкий и более прочный. При этом дает дополнительный объем. Поэтому толстый файбергласс рекомендуется использовать для наращивания ногтей и донаращивания углов. Такой материал лучше формирует свободный край, и тот не заламывается при носке.
Тонкий файбергласс имеет большую гибкость, не дает объема, но остается таким же прочным в носке. Его рекомендуется использовать для ремонта наращенных ногтей, достраивания стенок и армирования архитектуры пластины.
В арсенале мастера должно быть и тонкое и толстое стекловолокно для возможности выполнения различных покрытий, а также комбинирования техник.
Плюсы и минусы
Как и любой материал, стекловолокно имеет ряд плюсов и минусов в работе и носке. Учитывай их сразу, чтобы адаптировать технологию для себя или клиентов.
Плюсы:
- Простота использования;
- Быстрота обработки ногтей материалом – экономия времени мастера;
- Подойдет и для новичков в наращивании;
- Низкая цена закупки и себестоимость при формировании цены на услугу клиентам;
- Прочность, легкость и гибкость материала в носке;
- Нет необходимости строить архитектуру ногтя, материал идеально ложится по форме пластины изначально, повторяя её изгиб;
- Легко выкладывается на ноготь, не требуется постановки форм;
- Не проваливается под тяжестью базы;
- Можно комбинировать с любыми другими видами материалов для ногтей – базой, гелем для наращивания;
- Отсутствие аллергических реакций на сертифицированный материал.
Минусы:
- Файбергласс полностью повторяет форму натурального свободного края и ногтевой пластины. Если она растет вверх или «клюет» вниз, она такой и останется при наращивании стекловолокном. Такую ситуацию придется исправлять дополнительными материалами для коррекции. Например, гелем или жесткой базой.
Инструменты и дополнительные материалы
Для работы с файберглассом потребуется перечень дополнительных инструментов и материалов, которые облегчат процедуру и дадут желаемый результат:
- Файбергласс нужной толщины;
- Ножницы для нарезки волокон. Должны использоваться только для этой цели, так как материал тупит острый край, и превращает инструмент в нерабочий по ногтевой пластине;
- Любой топ без липкого слоя для скрепления волокон между собой;
- Апельсиновая палочка;
- Перчатки;
- База для гель-лака или гель для наращивания;
- Для наращивания потребуется зажим или обратный пинцет для формирования арки ногтя;
- Карандаш или фломастер;
- Файлик или плотная полиэтиленовая подложка.
Особенности технологии
Все манипуляции с материалом выполняй в перчатках. Почему это важно? Материал содержит стекло, острый в нарезке. Мелкие частички могут впиваться в кожу, вызывая раздражение.
Подготавливая материал к фиксации на ногти, его необходимо предварительно нарезать участками нужной длины и скрепить волокна между собой топом без липкого слоя. Так они не рассыпятся. Получатся пучки, которые затем фиксируются на пластины.
Для армирования нужно будет нарезать материал очень мелкими кусочками длиной по несколько миллиметров. Для этого этапа потребуется файлик или плотная клеенчатая подложка.
Волокно складывается по длине в два раза и посередине «раскатывается» карандашом или фломастером до получения плоской пластины. Можно помогать себе разделять волоски апельсиновой палочкой. При этом они всё же должны плотно прилегать друг к другу, без пробелов по ширине, иначе топ не соединит их между собой.
Полученную плоскую пластину из раскатанных волокон необходимо промазать по ширине топом без липкого слоя. Далее снимаем с лампы дно и полимеризуем топ для фиксации «полотна». Топ будет хорошо отделяться от файла или плотной полиэтиленовой подложки.
Чтобы разметить волокно одной упаковки файберглассса на рабочие отрезки и сделать скрепленные топом заготовки заранее, используй нижние формы для наращивания ногтей. Они содержат сетку-разметку длины. Для этого наклейка отделяется от основы, сгибается, склеивается вдвое, и со стороны теперь хорошо видно возможную максимальную длину, которую может запросить клиент.
Прикладываем полученный шаблон к пучку волокон и скрепляем их топом через равные промежутки этой длины. Каждый раз раскатываем пучок карандашом для получения «пластины из волокон». Теперь вся длина файбергласса промазана топом через равные участки.
При работе с клиентом, тебе потребуется просто отрезать нужное количество заготовок и выполнять наращивание или укрепление. Так мы экономим время и усилия.
Чтобы разрезать файберглассовые заготовки, их необходимо хорошо натянуть между пальцами, разровнять, и ровно срезать ножницами. Один край будет скреплен топом, а второй расходиться веером и даже распушиваться. Теперь его удобно ровно распределять по ногтевой пластине клиента.
Для дополнительного укрепления или армирования ногтей файбергласс может выступать в качестве аналога акриловой пудры. Для армирования материал нарезается очень мелкими кусочками, стригущими движениями, и складывается в специальную баночку с подложкой на дне из файла или бумаги. Материал нарезается очень легко.
После самостоятельной нарезки необходимо протереть рабочее место и файл-подложку влажной салфеткой, чтобы улетевшие частички не попадали на кожу, вызывая раздражение.
Файбер база от Dance Legend, и другие ей подобные, содержат в себе мелкие частички стекловолокна и являются уже готовым аналогом этой заготовки.
Подготовка ногтей к покрытию
Этот этап является обязательным для прочной фиксации файбергласса и создания ноской основы. Любой искусственный материал требует специальной подготовки, чтобы не возникало сколов и отслоек.
Пошаговая инструкция подготовки для наращивания стекловолокном:
- Снятие старого покрытия
- Выполнение аппаратного или обрезного маникюра, придание ногтям формы;
- Обработка пластин бафом или пилкой для поднятия чешуек с целью дальнейшего улучшения сцепления;
- Обезжиривание. Тщательно прорабатываем зону под кутикулой и боковыми валиками;
- Дегидратация. Обработка бондером, препаратом Nail Prep или Fresher. Могут иметь разные названия в разных марках. Цель – удалить лишнюю влагу с поверхности пластины. Она должна приобрести легкий белесоватый налет.
- Нанесение праймера. Служит для улучшения сцепления натурального и искусственного материала. Можно сравнить по действию с двусторонним скотчем. Праймер на натуральный ноготь наносится только на свободный край. Для этого используется бескислотный вариант. Кислотный праймер на натуральный ноготь – только для клиентов с гипергидрозом.
В каких случаях применяется файбергласс: техники использования
Существует шесть самых распространенных случаев, когда рекомендовано использование стекловолокна. В большинстве из них оно является аналогом геля или акрила, и отличается лишь легкостью в обращении и большей пластичностью в носке.
Рассмотрим все случаи с пошаговыми инструкциями по применению.
Для наращивания свободного края, длины ногтя
В этом случае не нужны специальные навыки моделирования, только базовые знания по выравниванию ногтевой пластины и как опиливать форму.
Мастеру потребуется пластичная база, которая обеспечивает лучшую сцепку с материалом. Если используется жесткая база, то лучше под неё положить слой пластичной базы для улучшения носибельности.
- Наносим базу вбивающими движениями на всю подготовленную ногтевую пластину. Тонким слоем;
- На самом краю наносим еще немного базы, создавая «полоску» средней толщины, чтобы не было зазоров между свободным краем и искусственным материалом;
- Берем заготовку-отрезок файбергласса, срезаем заполимеризованный участок с топом, немного распушив волокна по ширине, и прикладываем к свободному краю;
- Апельсиновой палочкой аккуратно распределяем волоски по всей ширине свободного края, фиксируем;
- Отправляем на сушку на рекомендуемое для базы время с учетом мощности лампы;
- Сверху наносим более плотный слой базы, обрабатывая и новый свободный край, сформированный файберглассом;
- Переворачиваем палец и промазываем базой волокна изнутри;
- Полимеризуем в лампе;
- Снимаем липкий слой снаружи и под пластиной;
- Придаем форму опилом с помощью пилки или твердосплавной фрезы;
- Выравнииваем пластину при необходимости, строим архитектуру;
- Если строится поперечная арка, используется зажим;
- Продолжаем нанесение декоративного покрытия.
Для достраивания стенок ногтя при отрастании или скручивании
Файбергласс позволяет придать пластине нужную форму, достроить недостающую плоскость боковых стенок, которые подворачиваются при отрастании.
Для донаращивания углов ногтей при сколах, надломах, опиле нужной формы
Во предыдущем и данном случае используется одинаковая техника. При скручивании стенки или отколе уголка выполняем следующие шаги:
- Наносим тонкий слой базы вбивающими движениями;
- Наносим еще полоску базы на свободный край;
- Отделяем от заготовки файбергласса несколько волосков, и апельсиновой палочкой крепим на зону скрутившейся стенки или скола кончика ногтя. Стекловолокно должно немного выходить за линию края в сторону, чтобы была возможность опила формы;
- Полимеризуем, наносим второй слой базы поверх пластины и под низ на стекловолокно. Снова полимеризуем;
- Придаем форму свободному краю по длине и в зоне точек вроста;
- При донаращивании стенок необходимо перевернуть палец и выпилить выступающую часть натурального ногтя изнутри твердосплавной узкой фрезой;
- Выравниваем.
Для армирования ногтевой пластины по всему периметру
Для армирования ногтей используется следующая техника:
- Файбергласс нарезается на мелкие частички или используется заготовка по вышеуказанной инструкции. Чем мельче кусочки, тем проще работать. Волоски не будут торчать из базы;
- Смешиваем файбергласс с пластичной базой (в соотношении 80% базы и 20% стекловолокна) на фольге или палитре;
- Дополнительной плоской кисточкой наносим заготовленный материал на ноготь, уделяя особое внимание стрессовым зонам;
- Полимеризуем в лампе;
- Сверху выполняем выравнивание обычной базой.
Для укрепления стрессовых зон ногтя, особенно при удлиненных формах
Потребуются заготовки, от которых отделяются тонкие полоски.
Этапы укрепления:
- Наносим тонкий слой базы;
- Отрезаем от заготовок тонкие короткие полоски, и равномерно укладываем на стрессовые зоны. Аккуратно фиксируем апельсиновой палочкой;
- Полимеризуем в лампе;
- Выполняем выравнивание.
Ремонт ногтевой пластины
При образовании скола на поверхности пластины, необходимо забафить эту зону, нанести небольшое количество базы, смешанной с нарезанным стекловолокном, и заполимеризовать.
Если трещина или залом образовалась на свободном крае, он «гуляет», то понадобится файбергласс, база и старые щипцы.
- Ими вырезаем зону трещины, создавая «мягкий угол» или треугольник.
- Зону ремонта подготавливаем бафом, обезжиривателем, дегидратором и праймером по окружности.
- Трещину промазываем базой, отрезаем немного стекловолокна и укладываем его поверх трещины. Апельсиновой палочкой распределяем, фиксируем.
- Наносим базу снизу ногтя на материал, полимеризуем;
- Придаем форму, снизу не выпиливаем без необходимости;
- Делаем выравнивание.
Если сравнивать стекловолокно с акрилом, то акрил – это пластик, а файбергласс – стекло. Он более прочный и не дает отслоек и сколов, так как содержит удлиненные и гибкие волокна.
Технология работы с файберглассом является аналогом наращивания и коррекции, выполняемым с помощью геля или акрила. Отличительные плюсы – легкость в работе даже для новичков, большая гибкость, пластичность и экономичность материала.
Остались вопросы по технологии? Напиши нам в комментариях.
Стеклопластик — самый популярный материал тюнинговиков всего мира. Дело в том, что, в отличие от всех иных материалов, стеклопластиковые детали можно изготовить чуть ли не в гараже на коленках. Дерево, в принципе, также не требует дорогого оборудования и специальных помещений, но изготавливать бампер или крыло из дерева более чем странно.
Стекловата используется людьми с начала прошлого века. Стекловолокно появилось лишь в 40-х годах. Этот материал уже давно применяется при строительстве лодок. Стеклопластик — достаточно универсальный материал. Можно изготовить тоненькую декоративную накладку или бампер, которым можно будет снег во дворе разгребать. Были прецеденты, когда в автомобиль с кузовом, изготовленным из стеклопластика, врезались простые, «стальные» автомобили и результат был не в пользу последних. Конечно, речь идет о специальных деталях, где осуществляется специальное упрочнение, но в любом случае стеклопластиковые детали — достаточно крепкая штука.
Что же такое стеклопластик? Если просто, то этот материал представляет собой стекловолокно, пропитанное некой смолой. Смолы бывают разные, для разных условий работы и необходимых характеристик готового изделия. Есть смолы, которые застывают при комнатной температуре, а есть такие, которым необходим нагрев. Смола и специальный катализатор (отвердитель) тщательно смешиваются в определенной пропорции, и затем этим составом пропитывается полотно, состоящее из особых стекловолокон. Сама смола достаточно хрупкая штука, и именно стекловолокно придает ей необходимую прочность и гибкость. Для получения изделий из стекловолокна часто приходится изготавливать специальные матрицы, но об этом далее.
Очень важно правильно подобрать пропорции смолы и катализатора. Если переборщить с последним, то смола застынет раньше, чем вы сможете закончить работу. Если недолить, то смола будет сохнуть слишком долго.
МАТЕРИАЛЫ
Смола, в принципе, вещь стандартная, но смолы разных фирм могут довольно сильно отличаться друг от друга по качеству. На свойства смол и на их рабочие параметры довольно сильно влияют температурные характеристики помещения, в котором производятся работы, и его проветриваемость.Порой для лучшего застывания матрицу с изделием помещают в специальную сушильную камеру. Это помогает значительно ускорить процесс получения готового изделия. Самые прочные изделия изготавливаются в автоклавах под большим давлением и высокой температурой.
Как было сказано выше, смолы — не столь крепкий материал, и стекловолокна выступают в качестве армирующего материала. Стекловолокно бывает различным и по толщине, и по структуре. Есть два основных типа: стекломат и стеклоткань. Стекломат состоит из хаотично расположенных волокон, а стеклоткань выглядит как обычная ткань. Наибольшее упрочнение дают различные марки стеклотканей. Стекломаты дают меньшую прочность, но они более легки в обработке и по сравнению со стеклотканью лучше повторяют форму матрицы.
Стекломат может быть очень тонким, воздушным (такой материал называют стек-ловуалью), а бывает толстым, как одеяло. Стекломаты различаются по толщине и плотности, но разделяют их по весу одного квадратного метра материала в граммах: 300, 450, 600, 900. Стекловуаль с плотностью 32 г/кв.м позволяет вывести поверхность очень высокой сложности, с большим количеством граней и резких переходов. Толстый мат (600 или 900) позволяет набрать толщину изделия и добиться необходимой прочности. Стоит отметить, что при создании толстых изделий работа проходит в несколько этапов. Выкладывается несколько листов для получения первого слоя и дается время на застывание. Затем дополнительно, уже на твердую поверхность, укладываются дополнительные листы мата для придания необходимой толщины. Если попытаться уложить сразу все слои, то велика вероятность, что готовое изделие покоробится, стянется.
Стеклоткани (иногда за характерное плетение их называют «рогожей») бывают разной толщины. Эти ткани также используются для придания жесткости и объема готовому изделию. Как и любая ткань, стеклоткань неодинаково работает при разнонаправленном растяжении. Поэтому для придания необходимой жесткости стеклоткань укладывается под разными углами. Качество стекловолокна также играет немаловажную роль. Оно должно хорошо пропитываться смолой и удерживать ее между волокнами.
Для придания изделиям с большими плоскостями прочности и стабильности, а также для снижения массы готового изделия применяются специальные вставки из нетканых материалов. Это материал из непрерывного полиэфирного волокна, содержащий в своей структуре микробаллоны. Он укладывается между несколькими слоями стекломата. Зачастую он вклеивается лишь армирующими полосками, а не большими полотнищами. К слову о прочности. Как это ни странно прозвучит, но чем меньше смолы в стекловолокне (при условии его полной пропитки и отсутствии пузырьков), тем прочнее будет готовое изделие и тем меньше окажется и его вес.
Часто можно услышать об автомобилях со стеклопластиковыми кузовными элементами, что они стойки к царапанью, так как окрашены в массе. Это не совсем так. Поцарапать их можно, но цвет сохранится. Происходит это потому, что при изготовлении деталей с качественной поверхностью поначалу в матрицу наносится декоративный слой гелькоута. Этот полиэфирный состав и освобождает изделия от дальнейшей покраски. Его можно подобрать по цвету или создать свой оттенок колеровочными составами. Кроме того, гелькоутный слой увеличивает срок службы изделия, защищает от воздействий окружающей среды и скрывает структуру стеклопластика. После того как гелькоут затвердел, укладывается стекловолокно и смола. Готовое изделие будет иметь ровную (зависит от качества матрицы), нужного цвета поверхность.
В этом процессе кроется один важный момент. Если слой гелькоута будет в одном месте слишком тонкий, то может случиться следующее: или в этом месте будет просвечивать структура стекловолокна, или гелькоут может вообще отойти и сморщиться. Поэтому крайне важно пользоваться правильными материалами и следовать технологии. Для равномерного нанесения гелькоута часто используют не кисти, а краскопульты. Так удается значительно сократить количество брака. Но для распыления гелькоут должен быть более жидким, чем для ручного нанесения.
МАКЕТ И МАТРИЦА
Для изготовления изделия из стеклопластика первое, что необходимо, — создать его макет. Собственно, макет нужен всегда, но при одноразовой работе иногда удается укладывать стеклоткань на временные распорки. Этот подход срабатывает только тогда, когда нет необходимости в создании качественной поверхности. К примеру, очень часто при изготовлении новых дверных панелей основу изготавливают из стеклопластика прямо на двери, защитив ее предварительно пленкой бумажного скотча, полиэтилена, воска и т. п. Плохое качество поверхности в данном случае мало кого волнует, так как затем на эту прочную стеклопластиковую корку клеится пористый материал, а на него кожа, ткань или что-то другое. Технология изготовления кузовных и декоративных изделий из стеклопластика и тех предметов, которые будут тиражироваться, несколько сложнее. Здесь не обойтись без макетирования и матрицирования.Макет будущего изделия может быть изготовлен различными способами: фанера, пластилин, пенопласт и т. д. От того, насколько правильно сделан макет, будет зависеть качество будущих изделий. Более того, если необходимо, чтобы у детали, которая будет затем создаваться, была идеально ровная поверхность, над ее качеством придется поработать уже на макете. Чем более гладким и ровным будет макет, тем меньше работы потребуется потом, при изготовлении и доведении матрицы.
Еще до создания макета необходимо понять, можно ли изготовить деталь целиком или нет. Дело в том, что при работе со стеклопластиками и другими подобными материалами необходимо, чтобы готовую деталь после застывания можно было вытащить из матрицы, ничего не повредив при этом. Возможно, деталь будет иметь такую форму, что ее придется изготавливать из нескольких частей, а затем скреплять их друг с другом, но выклеить шар через угольное ушко вряд ли получится.
Матрица создается по макету. Это самый ответственный момент. Прежде всего макет вощится, т. е. покрывается тонким слоем воска. Эту процедуру можно сравнить с полировкой автомобиля. После того как макет подготовлен, на него наносится слой специального матричного гелькоута. Это покрытие в дальнейшем позволит вывести поверхность матрицы практически до зеркального блеска. Матричный гелькоут гуще, чем обычный, и ложится более толстым слоем.
После того как встанет этот слой, начинается укладывание стекломата. Сначала -тонкая стекловуаль. Она позволит точно повторить все изгибы и контуры макета. Далее желательно дать подсохнуть первому слою. Затем уже можно выложить еще несколько слоев более толстого мата, но сразу набирать толщину не стоит, иначе матрицу может повести (изогнуть и покоробить). При создании матриц на простые детали можно упростить процедуру. Тут главное — опыт.
Если матрица будет разъемной, то при ее изготовлении делаются специальные перегородки вокруг макета, разделяющие его на сегменты. Выложив основной, после его застывания перегородки вынимаются и, обработав кромки первого сегмента матрицы, выкладываются остальные. Для правильного позиционирования сегментов друг относительно друга в первом при формовании делаются специальные ямки. Когда будут формоваться следующие сегменты, эти ямки будут заполнены смолой и стекловолокном, и появятся бугорки. Эти пары и позволят при будущем использовании правильно скрепить различные части матрицы воедино. Для скрепления сегментов матрицы в ребрах всех отдельных частей сверлятся отверстия под крепежные болты. Для того чтобы матрица была прочной и хорошо держала форму, после ее изготовления, прежде чем вынуть макет, к матрице приформовывают ребра жесткости. В зависимости от ее размеров это может быть прочный стальной каркас или небольшие фанерные или деревянные ребра. Готовая матрица, если макет был изготовлен аккуратно, может и не потребовать дополнительной обработки, но зачастую приходится выводить поверхности, шлифовать и полировать матрицу до блеска. Только тогда можно получить идеальную деталь. А к кузовным элементам вообще нужно особое внимание.
Затем начинается долгий процесс вощения. Матрицу приходится тщательно натирать воском несколько раз с перерывами. Воск нужно не просто намазывать, а растирать до получения тонкой, гладкой, невидимой пленки. Если этого не сделать, то поверхность готового изделия будет не гладкой, а шершавой.
После, а порой и вместо вощения иногда используют специальные жидкости, которые, высыхая, создают пленочное покрытие, предотвращающее попадание смолы или гелькоута на матрицу, чего никак нельзя допускать. Как нельзя и царапать ее поверхность. В противном случае смола может «намертво» прирасти к матрице, и тогда процедуру шлифовки, полировки и вощения придется повторять снова. Порой используют особые составы, обработав которыми матрицу можно снимать с нее до 100 изделий, но старый добрый воск всегда остается самым понятным и надежным средством.
Процесс создания матрицы, описанный выше, является довольно распространенным вариантом, используемым в большинстве тюнинговых фирм, но это не означает, что нет иных способов. Существуют компьютерные технологии, станки с ЧПУ, позволяющие по виртуальной модели вырезать из любого материала любой макет или уже готовые пресс-форму или матрицу. Но это уже промышленный, не гаражный уровень.
Собственно, далее можно приступать к изготовлению деталей. Слой гелькоута в принципе не обязателен, но, во-первых, он придает более законченный вид готовому изделию, а будучи цветным, позволяет сэкономить на покраске или вообще от нее отказаться, а во-вторых, он защищает матрицу от стекловолокна, которое на самом деле очень даже абразивно, т. е. царапает.
ТЕХНОЛОГИИ
Технологий производства изделий из стекловолокна существует несколько. Стоит сразу оговориться, что эти методы используются и при работе с другими армирующими материалами, такими, как карбон, кевлар, другие тканые материалы и их сочетания.Ручное (контактное) формование. Этот способ самый простой и дешевый (если не считать затрат на квалифицированную рабочую силу). Пропитка стекловолокна осуществляется валиком или кистью, которые должны быть стойкими к смолам. Волокно или сразу укладывается в форму, или уже после пропитки. Обработка стекловолокна разбивочными валиками способствует лучшему распределению смолы между волокнами. Затем укаточными валиками производят окончательную укатку стеклоткани, выдавливая пузырьки воздуха и равномерно распределяя смолу по всему объему. Крайне важно не допустить, чтобы под слоем стеклоткани оставались пузырьки воздуха. Если изделие застынет с таким браком, это место будет ослаблено вплоть до возможного сквозного продавливания. Такие брачки также могут помешать дальнейшей обработке изделия, потребовать его восстановления или полной замены. В любом случае будут затрачены дополнительные материалы, труд, а также деньги.
Ручной метод может быть несколько механизирован. Существуют смесители, подающие смолу с катализатором через валик, и иные приспособления. Но укатывать все равно приходится своими руками.
Достоинство ручного метода вполне очевидно: просто и дешево. Но любая экономия может иметь и обратную сторону. Качество готовых изделий очень сильно зависит от квалификации рабочих. И условия труда при таком подходе довольно вредные. Кроме того, очень сложно добиться большой производительности. Однако для небольших фирм и малых объемов работы этот метод самый подходящий.
Метод напыления рубленого ровинга. Этот подход куда более технологичен. В нем используется не стекловолокно, а стеклонить, которая подается в измельчитель специального пистолета, где рубится на короткие волокна. Затем пистолет «выплевывает» их вместе с порцией смолы и катализатора. В воздухе все смешивается и наносится на форму. Но после этой процедуры все равно массу необходимо прикатать, чтобы удалить пузырьки. Далее отвердевание происходит как обычно.
Такой способ выглядит очень заманчиво и просто. Казалось бы, стой и поливай из шланга. Но есть один существенный недостаток, из-за которого этот способ не столь популярен, — слишком большой расход смолы. Изделие получается очень тяжелым, и, так как волокна не переплетены друг с другом, механические свойства такого стеклопластика несколько хуже. Кроме того, к вредным парам смол подмешивается взвесь мелких частиц стекла от измельчителя, очень вредных для легких человека.
Метод намотки. Этот специфический метод предназначен для изготовления пустотелых круглых или овальных секционных компонентов, типа труб или резервуаров. Таким образом делаются парусные мачты, удочки, рамы велосипедов, глушители автомобилей и т. д. Стекловолокна пропускаются через ванну со смолой, затем через натяжные валики, служащие для натяжения волокна и удаления излишков смолы. Волокна наматываются на сердечник с необходимым сечением, угол намотки контролируется отношением скорости движения тележки к скорости вращения. Как намотка нитки на шпульку швейной машинки. В результате получаются крепкие и легкие изделия.
И достоинства, и недостатки этого метода очень близки. Им не сделать автомобильное крыло, но сделать мачту корабля или даже кардан другими способами не менее сложно.
Метод препрегов. В данном случае используются не отдельные смола и ткань, а так называемые препреги — предварительно пропитанная смолами стеклоткань. Стекловолокно предварительно пропитывается предката-лизированной смолой под высокой температурой и большим давлением. При низких температурах такие заготовки могут храниться недели и даже месяцы. При этом смола в пре-прегах находится в полутвердом состоянии. При формовании препреги укладываются в матрицу и закрываются вакуумным мешком. После нагрева до 120-180°С смола переходит в текучее состояние, и препрег под действием вакуума принимает нужную форму. При дальнейшем повышении температуры смола застывает.
Вся проблема этого метода в необходимости нагревательного оборудования, особенно автоклава. По этой причине изготавливать большие детали очень сложно. Но и плюсы очевидны. Использование вакуума позволяет значительно снизить вероятность появления воздушных пузырьков и существенно сократить долю смолы в готовом изделии.
Существуют и иные технологии — пултрузия, RFI, RTM и др. — практически на все случаи жизни. Выбор той или иной технологии зависит от необходимых объемов, сложности изделия и количества денег у организатора такого производства.
ВЫВОДЫ
Что дает стеклопластик? Прежде всего — вес. И хотя для создания по-настоящему крепких деталей порой приходится делать их толстыми, а это лишние килограммы, но, в отличие от стали или алюминия, стеклопластик способен возвращаться в исходную форму после ударов, не повлекших за собой разрушения элемента. И при ремонте деталей из стеклопластика понятие «кузов-ня» приобретает несколько иной смысл. Незначительные трещины могут быть заклеены изнутри смолой, с наложением листа стеклоткани или мата. Большие повреждения можно восстановить, уложив деталь снова в матрицу и восстановив по порядку нужный сегмент. Но такой способ может не дать хорошего качества, и велика вероятность повреждения матрицы, а этого никак нельзя допускать. Проще сделать новый элемент. Хотя стеклопластиковые детали можно восстанавливать и старым способом: шпаклевка, шпатель, шкурка и вода.К недостаткам следует отнести высокую стоимость материалов. Но что самое плохое -большая токсичность. При работе с этим материалом крайне важно соблюдать технику безопасности. Желательно пользоваться респиратором, поскольку пары эпоксидных смол совсем небезвредны. Как бы то ни было, стеклопластик и по сей день остается самым популярным материалом мирового тюнинга. И хотя разнообразные кевлары, карбоны, пенополиуретаны, базальтовое волокно и т. п. начинают все сильнее его теснить, думается, что стеклопластик еще долго будет востребован.
Что такое стекловолокно?
+90 232 376 88 22
info @ polser.ком
Пн-Пт: 09: 00-18: 00
TÜRKÇE
- ДОМОЙ
- КОМПАНИЯ
- назад
- ПРОФИЛЬ КОМПАНИИ
- ПОЛИТИКА КАЧЕСТВА
- ЭКСПОРТ
- ВИДЕНИЕ МИССИИ
- HR
- ТОВАРЫ
- назад
- СТРОИТЕЛЬНАЯ ПРОМЫШЛЕННОСТЬ
- назад
- Аэроплан
- ARMORPAN
- DECOLITE
- DECOSER
- DURADECK
- DURASER
- DURAPAN
- DURAWIND
- FIBRALAM
- FIBERWALL
- ЖАРОВНЯ
- ISOBOARD
- Isolite
- KAMUFLAM
- ИНДУСТРИЯ ОХЛАЖДЕНИЯ БАШНЕЙ
- назад
- DURASER
- ЖАРОВНЯ
- СЕЛЬСКОЕ ХОЗЯЙСТВО И ЖИВОТНОВОДСТВО
- назад
- DECOSER
- DURAPAN
- DURASER
- ISOBOARD
- SERALAM
- ГИГИЕНИЧЕСКАЯ ПРОМЫШЛЕННОСТЬ
- назад
- DECOSER
- ISOBOARD
- ПИЩЕВАЯ ПРОМЫШЛЕННОСТЬ
- назад
- DECOSER
- ISOBOARD
- АВТОМОБИЛЬНАЯ ПРОМЫШЛЕННОСТЬ
- назад
- DECOSER
- FRIGOSER
- GRP ДВЕРНЫЕ ПАНЕЛИ
- ISOBOARD
Что такое стекловолокно? (с картинками)
В самом строгом смысле, стекловолокно является товарным знаком компании Owens Corning, изобретенной в 1938 году и продаваемой в качестве средства для домашней изоляции (Fiberglas). В то время как домашняя изоляция остается одним из наиболее распространенных применений, само название стало общим термином для любого материала, содержащего тонкие волокна стекла, сформированные в тканый слой или используемые в качестве армирования.

«Стекло» из стекловолокна — это то же самое основное вещество, которое используется в окнах и стеклянной посуде. Расплавленное стекло экструдируется через ультратонкие отверстия, измеряемые в микронах, в результате чего образуются нитевидные образования, которые можно сплести вместе для образования грубая ткань или заплатка. Затем к этому материалу можно добавлять различные смолы, что позволяет ему формироваться и прессоваться в формы.Результатом является термостойкая, легкая панель, идеально подходящая для электронных плат или опорных конструкций для сложных машин.

Стекловолокно, смешанное со смолами, также может быть использовано для формирования корпуса гоночных автомобилей или других нестандартных конструкций. Ремонт может быть сделан с помощью коммерческого продукта под названием Bondo, который по существу представляет собой стекловолоконную ленту, смешанную со смолой быстрого отверждения.Когда этот материал используется для кузовных работ, его можно гладко отшлифовать и покрасить в соответствии с остальной частью автомобиля. Он может не иметь присущей стали прочности на растяжение, но квалифицированный специалист по кузовному ремонту часто может без проблем совмещать участок, отремонтированный из стекловолокна и смолы, с остальной частью автомобиля.
В большем масштабе стекловолокно может быть смешано с другими материалами для формирования толстой изолирующей прокладки.Подушка, содержащая стекловолокно, прикреплена клеем к алюминизированной подложке. Затем материал делится на стандартные ширины, которые будут располагаться прямо между вертикальными стойками (открытыми опорными плитами) незаконченной стены. Большое количество стекловолокна упаковывается в пространство между наружной стеной и внутренней стеной. Как только весь изоляционный материал будет размещен, панели гипсокартона могут быть установлены, чтобы закончить комнату.
Стекловолокно как строительный и изоляционный материал очень универсален, но его не всегда легко и безопасно использовать.Поскольку основным ингредиентом является настоящее стекло, часто образуются микроскопические частицы стеклянного порошка или осколков. Те, кто устанавливает изоляцию, должны всегда носить перчатки, защитные очки и маски. Осколки стекла и пудра могут остаться на коже даже после нескольких стирок. Эти частицы могут быть очень раздражающими для легких и рук и чрезвычайно вредными для глаз. Защитный барьер для крема для рук может помочь предотвратить накопление порошка из стекловолокна.
Если вы работаете со сжатой формой из стекловолокна (т.е.е. электронные доски), сжатый воздух может быть лучшим способом удаления остатков. Не прикасайтесь к глазам или другим чувствительным областям при работе с этим материалом в любой форме. Если порошок попал в глаза, используйте большое количество чистой воды или одобренного средства для промывки глаз и обратитесь к глазному врачу для экстренного осмотра.

Стекловолокно — это форма армированного волокном пластика, где стекловолокно является армированным пластиком. Возможно, именно поэтому стекловолокно также называют стеклопластиком или стеклопластиком. Стекловолокно обычно сплющивают в лист, случайным образом укладывают или вплетают в ткань. В соответствии с использованием стекловолокна, стекловолокно может быть изготовлено из различных типов стекла.
Стекловолокно легкое, прочное и менее хрупкое.Лучшая часть стекловолокна — это его способность формоваться в различные сложные формы. Это в значительной степени объясняет, почему стекловолокно широко используется в ваннах, лодках, самолетах, кровлях и других применениях.
В этой статье мы подробнее поговорим о типах стекловолокна, а также их свойствах и применениях. Давайте начнем.
Типы и формы стекловолокна:
В зависимости от используемого сырья и их пропорций для производства стекловолокна, стекловолокно можно классифицировать по следующим основным типам:
- A-стекло : стекло также называют щелочью стекло и устойчив к химическим веществам.Благодаря составу стекловолокна, он близок к оконному стеклу. В некоторых частях мира он используется для изготовления технологического оборудования.
- C-стекло : C-стекло обладает очень хорошей стойкостью к химическому воздействию и также называется химическим стеклом.
- E-стекло : оно также называется электрическим стеклом и является очень хорошим изолятором электричества.
- AE-стекло : это стекло, стойкое к щелочам.
- S стекло : оно также называется структурным стеклом и известно своими механическими свойствами.
Стекловолокно выпускается в различных формах для различных применений, основными из которых являются:
- Стекловолоконная лента : Стекловолоконные ленты изготовлены из стекловолоконной пряжи и известны своими теплоизоляционными свойствами. Эта форма стекловолокна находит широкое применение в оберточных сосудах, горячих трубопроводах и тому подобном.
- Стеклоткань : Стеклоткань гладкая и доступна в различных вариантах, например, из стекловолокна и стекловолоконной нити.Широко используется в качестве теплозащитных экранов, в противопожарных шторах и других.
- Стекловолоконная веревка : Канаты сплетены из стекловолоконной пряжи и используются для упаковочных целей.
Свойства стекловолокна
- Механическая прочность : Удельное сопротивление стекловолокна выше, чем у стали. Таким образом, он используется для создания высокопроизводительных
- Электрические характеристики : Стекловолокно является хорошим электрическим изолятором даже при небольшой толщине.
- Несгораемость : Так как стекловолокно является минеральным материалом, оно естественно негорючее. Он не распространяет и не поддерживает пламя. Он не выделяет дыма или токсичных продуктов при воздействии тепла.
- Стабильность размеров : Стекловолокно не чувствительно к изменениям температуры и гигрометрии. Обладает низким коэффициентом линейного расширения.
- Совместимость с органическими матрицами : Стекловолокно может иметь различные размеры и может сочетаться со многими синтетическими смолами и некоторыми минеральными матрицами, такими как цемент.
- Не гниет : Стекловолокно не гниет и не подвергается воздействию грызунов и насекомых.
- Теплопроводность : Стеклопластик обладает низкой теплопроводностью, что делает его очень полезным в строительной промышленности.
- Диэлектрическая проницаемость : Это свойство стеклопластика делает его пригодным для электромагнитных окон.
Применение стекловолокна в различных отраслях промышленности
Материалы с высокотемпературной изоляцией обеспечивают эффективный тепловой барьер для промышленных прокладок.Поскольку стекловолокно долговечно, безопасно и обладает высокой теплоизоляцией, стекловолокно является одним из наиболее предпочтительных материалов в промышленных прокладках. Они не только обеспечивают лучшую изоляцию, но также помогают защитить оборудование, сохранить энергию и обеспечить безопасность профессиональной рабочей силы. Возможно, именно поэтому стекловолокно широко используется в следующих отраслях промышленности:
- Производство напитков : Решетка из стекловолокна используется во многих областях, таких как линии розлива и варочные цеха.
- Автомойки : В последнее время стекловолоконная решетка широко используется для защиты от ржавчины и для придания контрастного цвета областям, которые ранее казались запрещенными. Это осветляет внутреннюю часть туннеля автомойки, делая машину более чистой, чем она была.
- Химическая промышленность : В этой отрасли стекловолоконная решетка используется для обеспечения защиты от скольжения встроенной зернистой поверхности и химически стойких свойств различных смоляных соединений. Используемые химические вещества соответствуют смолам.
- Градирни : Поскольку градирни всегда влажные, их необходимо защищать от ржавчины, коррозии и других проблем безопасности. Из-за превосходных свойств стекловолокна, он используется в этих башнях в качестве экранирования, чтобы держать людей и животных подальше от опасных зон.
- Доки и пристани для яхт : Доки подвергаются коррозии, коррозии и повреждению от соленой морской воды. Итак, стекловолокно используется здесь для защиты.
- Пищевая переработка : На заводах по переработке курицы и говядины стекловолоконная решетка используется для защиты от скольжения и для удержания крови, которая вызывает коррозию.Большинство областей пищевой промышленности также используют стекловолокно, поскольку другие материалы решетки не подходят.
- Фонтаны и аквариумы : фонтаны и аквариумы всех размеров используют стекловолокно для поддержки горных пород, чтобы способствовать циркуляции и фильтрации из-под скал. В больших общественных фонтанах стекловолоконная решетка используется для защиты распылительных коллекторов и источников света от повреждения. Это также не дает людям утонуть в фонтанах.
- Производство : Встроенная зернистая поверхность стекловолоконной решетки обеспечивает сопротивление скольжению в местах с повышенной влажностью или в местах, где присутствуют гидравлические жидкости или масла.
- Металлургия и горнодобывающая промышленность : Стекловолоконная решетка используется в областях электронного рафинирования, подверженных химической коррозии. Другие решетки не могут быть использованы здесь.
- Производство электроэнергии : Во многих областях энергетики, таких как нефтебазы, скрубберы и другие, используется стекловолокно. Причиной этого является непроводящее свойство стеклопластика.
- Установки для нанесения гальванического покрытия : В этом приложении используется стекловолоконная решетка из-за противоскользящего свойства поверхности.
- Целлюлозно-бумажное производство : Свойство стекловолокна, делающее его стойким к химической коррозии, полезно на целлюлозно-отбеливающих предприятиях. В последнее время стекловолокно используется во многих областях благодаря его коррозионной стойкости и противоскользящим свойствам.
- Автомобильная промышленность : Стекловолокно широко используется в автомобильной промышленности. Практически у каждого автомобиля есть стеклопластиковые компоненты и обвесы.
- Aerospace & Defense : Стекловолокно используется для производства деталей для военной и гражданской аэрокосмической промышленности, включая испытательное оборудование, воздуховоды, кожухи и другие.
Узнайте больше о портфеле Phelps Fiberglass
Стекловолокно является важным компонентом целого ряда отраслей, включая очистные сооружения, ОВК, противопожарные и нефтяные месторождения. Чтобы узнать больше о стекловолокне и его применениях, позвоните в Phelps @ 1-800-876-SEAL сегодня, чтобы получить более подробную информацию, и ознакомьтесь с ассортиментом стекловолокна Phelps.
Как делать стекловолокно Как и Pro
Стекловолокно, как термин, действительно является неправильным. Стекловолокно является одним из многих материалов, которые можно использовать вместе со смолой (пластиком) для создания прочной и легкой композитной структуры. Эти материалы включают стекловолокно (конечно), ткань (хлопчатобумажную или искусственную), углеродное волокно, нетканое стекло или углеродный мат, койр (кокосовое волокно), модал (волокно бука), бамбук и даже конопляное волокно.
На самом деле то, что большинство людей называют стекловолокном, правильно называют Fibre Reinforced Plastic (FRP).Это композитный материал , очень похожий на углепластик (CFRP), столь популярный сегодня, но FRP предшествует углеродному волокну как минимум на семьдесят лет.
Одним из самых ранних применений FRP были военные США при изготовлении вкладышей для шлемов. (см. рисунок внизу справа для лайнера времен Второй мировой войны)
После войны возвращающиеся солдаты начали экспериментировать с материалом в виде кузовов автомобилей и корпусов лодок. Парусники были одними из первых предметов, построенных из этого материала, а несколько лет спустя — водными судами.Потому что так мало было известно о силе FRP в те годы, большинство этих предметов были «перестроены». Корпуса лодок и кузовов автомобилей, изготовленные в 50-х и 60-х годах, до сих пор практически не разрушаются по своей силе.
Идеальный материал для хобби
Во многих отношениях это идеальный материал для любителей. Приложив немного терпения, его довольно легко использовать, и большая часть ваших усилий уходит на подготовку, если не на фактическое создание предмета. Никаких специальных инструментов не требуется. Фактически я рекомендую использовать старые контейнеры для пищевых продуктов для смешивания смолы и покупать или использовать дешевые щетинные кисти, пластиковые мастерки и / или деревянный дюбель для нанесения смолы.
Ловкость не требуется
Ловкости не так много. Если вы можете выложить лист ткани и удалить все морщины, то вы на полпути. Если вы можете лежать на густой, похожей на краску жидкости, не оставляя после себя пузырьков, вы на сто процентов пройдете путь. Это действительно довольно легко.
Единственный другой «ингредиент» — это терпение в ожидании затвердевания смолы.
Использует
FRP можно использовать для ремонта кузова, ремонта лодки или даже для создания новых объектов, которых раньше не было.Также можно использовать FRP для создания форм для других объектов FRP. Некоторые примеры использования FRP в прошлом включают ковшовые стулья Eames, абажуры, декоративные перегородки, стены теплиц и дверные панели — это лишь некоторые из них.
Если вы когда-либо сидели или сидели в кресле в стиле ведра Имса, вы знаете, насколько они сильные и легкие.
Прочность
Армированный волокном пластик, по некоторым оценкам, в шесть раз прочнее стали при том же весе в материалах. Фактически, он достаточно прочен для использования в бассейнах из стекловолокна (вода достаточно тяжелая) и даже в зданиях из стекловолокна.